Układy blokowe projektu Kozienice
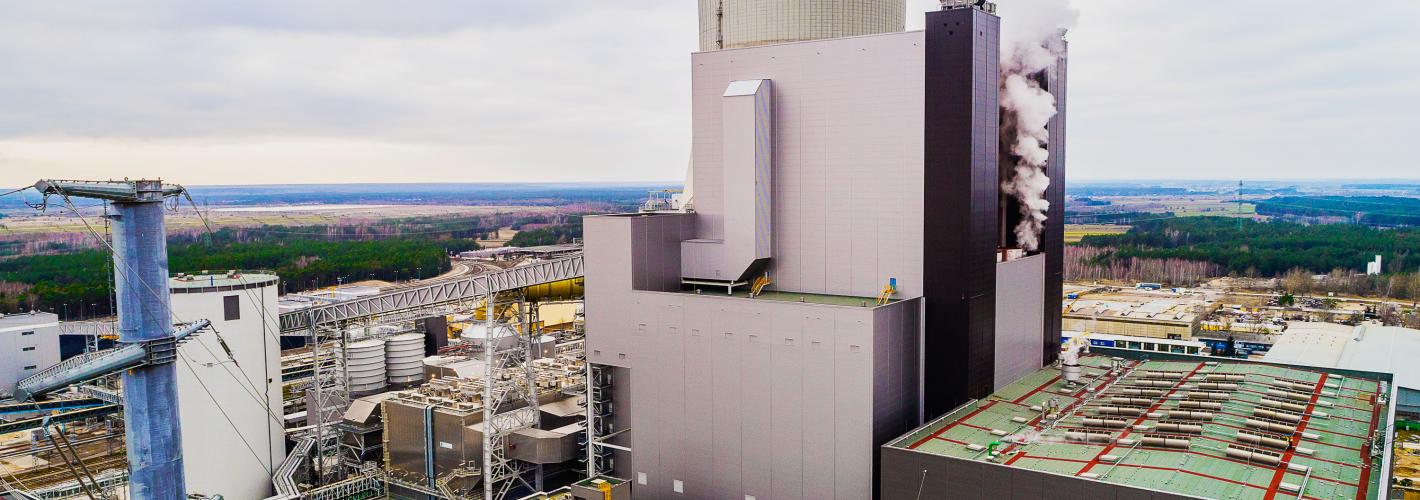
Źródło wody surowej
Źródłem wody surowej dla potrzeb uzupełnienia układu chłodzącego jest woda pobierana rzeki Wisły. Woda surowa pobierana jest za pomocą układu pomp, których wydajność jest płynnie regulowana przy pomocy przemienników częstotliwości w zależności od zapotrzebowania na wodę uzdatnioną.
Woda surowa z Wisły do Stacji Przygotowania Wody (SPW) przesyłana jest rurociągiem DN700. W SPW znajduje się rozdział kolektora DN700, na cztery kolektory DN300 – po dwa do każdego ciągu technologicznego.
Wydajność instalacji
Wydajność nominalna netto każdego z dwóch reaktorów wynosi 1 200 m3/h z uwzględnieniem odpowiedniej rezerwy dla wydajności maksymalnej.
Technologia uzdatniania wody
Proces przygotowania wody uzupełniającej do obiegu chłodzącego oparty jest o dekarbonizację wody surowej przy użyciu systemu Reaktora Wielokomorowego.
Proces technologiczny jest realizowany w następujących po sobie hydraulicznie połączonych komorach: Koagulacja „Komora kontaktowa, flokulacja i dekarbonizacja”. Sedymentacja wraz z dozowaniem odpowiednio dobranych dawek środków chemicznych.
Do RW dozowane są następujące chemikalia:
- mleko wapienne,
- koagulant – PIX-113,
- polielektrolit.
W budynku Stacji Przygotowania Wody znajdują się ponadto układy pompowe pełniące funkcję przesyłu wody zdekarbonizowanej (uzdatnionej) dla potrzeb:
- uzupełniania zbiorników wody ppoż.,
- chłodzenia sprężarek w sprężarkowni głównej blokowej,
- technologicznych blokowych tj.: IOS, zdmuchiwacze sadzy, odżużlanie, pomocniczo dla układów technologicznych w kotłowni.
Instalacja oczyszczania spalin bloku to nowoczesna instalacja spełniająca europejskie normy dotyczące stopnia redukcji zanieczyszczeń.
Spaliny z komory paleniskowej kotła przechodzą kolejno przez:
- instalację DeNOx typu high dust redukującej metodą katalityczną tlenki azotu, NO, NO2 i NO3
- elektrofiltry – wychwytujące cząstki stałe w spalinach metodą elektrostatyczną. Wychwytywane w nich tzw. popioły lotne są transportowane rurociągami do zbiorników popiołu wykorzystywane jako produkt rynkowy w przemyśle cementowym i materiałów budowlanych
- instalację odsiarczania spalin metodą Wet FGD, której produktem ubocznym jest gips wykorzystywany również jako produkt rynkowy. Sercem instalacji, gdzie następuje redukcja ze spalin SiO2 jest absorber, z wylotu którego oczyszczone spaliny dostają się charakterystycznym okrągłym kanałem o średnicy 10 m do chłodni kominowej.
Stąd w architekturę bloku energetycznego wpisane są olbrzymie, żelbetowe o cylindrycznej konstrukcji trzy zbiorniki retencyjne popiołów o pojemności 20 tys. m3 każdy, oraz żelbetowy silos na gips . Oba te obiekty wyposażone są w nowoczesne urządzenia do załadunku na cysterny samochodowe i kolejowe.
Dane charakterystyczne Kotłowni
- Kocioł - serce bloku 1 075 MWe
- Na fundamenty kotłowni zużyto ponad 22 tys. m³ betonu w ciągłym betonowaniu przy wykorzystaniu zlokalizowanych przy budowie węzłów betoniarskich o wydajności 165 m³ betonu na godzinę. Co 4 minuty, przez 7 dni betonomieszarki dowoziły wysokiej wytrzymałości beton do pomp ustawionych przy szalunkach
- Kocioł parowy typu Benson na parametry nadkrytyczne
- Kocioł przepływowy, bezwalczakowy
- Ciężar Kotła - ok 6 tys. ton
- Łączna długość rur wężownic kotła - 1 800 km
- Przepływ pary 3 tys. t/h
- Ilość węgla mielonego w młynach to 100 kg/sek.
Dane charakterystyczne:
- Turbozespół - największa jednostka wytwarzająca energię elektryczną w Polsce
- Waga generatora - 490 ton
- Długość generatora - 14,5 m
- Średnica generatora - 4 m
- Masa części wirującej (stojan + generator - ponad 1 800 ton)
- Masa turbozespołu (turbina + generator - ponad 3 500 ton)
- Długość turbiny - 39 m
- Turbiny czterokadłubowa - 4 - (WS, SP i 2x NP)
- Zbiornik wody zasilającej o pojemności prawie 1 000 m3 ma długość 75 m i średnicę 3,75 m
- Ciężar rurociągów- 1 157 ton
- Ciężar armatury- 248 ton
- Ciężar zamocowań rurociągów - 294 tony
Dane charakterystyczne:
- średnia planowana dobowa dostawa węgla - 9 600 ton (4 składy po 40 wagonów 60 ton każdy)
- pojemność placów składowych - 363 000 ton
- składowisko węgla nr 1UEF
- 347 x 53 m, H=17,5 m 192 000 ton
- składowisko węgla nr 2UEF347 x 50 m H =16,0 m 171 000 ton
- długość tras przenośników taśmowych - 3 306 m
- wydajność urządzeń transportowych - 1 600 t/h
- liczba obiektów budowlanych - 25
- najniżej posadowiony obiekt - stacja przesypowa 6.6.1 - 17,7 m
- najdłuższa trasa przenośników taśmowych - most skośny 6.5 - dł. 302 m z poziomu 0 m na poziom +63,2 m
- obszar - ok. 80 000 m2 (8ha)
Urządzenia technologiczne:
- wywrotnica wagonowa 1 szt.
- wygarniacz kołowy 2 szt.
- urządzenia przetokowe 8 szt.
- przenośnik taśmowy 20 szt.; 1 400 mm; 3,15 m/s
- separator elektromagnetyczny 6 szt.
- analizator wartości opałowej 4 szt.
- próbopobiornik 4 szt.
- waga taśmowa 4 szt.
- zespół do legalizacji wag 2 szt.
- przesiewacz rolkowy 2 szt.
- zsuwnie 2-drogowa 18 szt.
- pługi zrzutowy 14 szt.
- zespół nagrzewnic rozmrażalni 1 kpl.
Instalacje:
- woda hydrantowa
- woda pitna
- kanalizacja deszczowa
- kanalizacja przemysłowa
- sprężone powietrze
- woda zmywna
- instalacja odkurzania
- instalacja detekcji pożaru
- instalacja mgły wodnej
- instalacja zamgławiania przesypów
- HVAC
- instalacja c.o
Zakres pracy instalacji odżużlania obejmuje odbiór żużla z Kotłowni, aż do punktu załadunku żużla na samochody – poprzez system przenośników oraz dwa zbiorniki magazynowe o pojemności 700 m3 każdy, lub przetransportowanie zawiesiny żużlowej do pompowni bagrowej.
Opróżnianie zbiorników odbywa się poprzez zabudowane pod każdym zbiornikiem urządzenie wygarniające a następnie poprzez rękawy załadowcze – bezpośrednio na samochody. Jest możliwy jednocześnie załadunek żużla na dwa samochody, z dwóch zbiorników, lub załadunek żużla z jednego zbiornika na samochód, a z drugiego poprzez zsuwnię zdawczą do zbiornika zawiesiny żużla. Oba układy są wyposażone w wagi taśmowe służące do dwóch niezależnych pomiarów ilości żużla podczas jego sprzedaży.
Zawiesina jest gromadzona w zbiorniku zawiesiny usytuowanym na poziomie ±0,0 m.
Wymieszana zawiesina za pomocą dwóch pomp bagrowych - Q = 50 m3/h każda będzie transportowana rurociągami DN125 do istniejącej pompowni bagrowej.
Instalację wykonano bazując na następujących założeniach:
- medium: mokry żużel o granulacji 0÷30 mm i zawartości wody do 30%
- czas ciągów transportowych: praca ciągła
- wydajność hydrotransportu zawiesiny żużla: 50 m3/h
- czas pracy pomp bagrowych dla hydrotransportu: praca okresowa
- ciśnienie transportu zawiesiny: 0,4÷0,6 MPa
UKŁAD ODPOPIELANIA ELEKTROFILTRÓW BLOKU NR 11
Popiół lotny z bloku jest wytrącany ze spalin w dwóch elektrofiltrach. Każdy elektrofiltr posiada 5 stref oraz 6 rzędów czyli 30 lejów. Wypad popiołu z jednego elektrofiltra wynosić będzie przy działających strzepywaczach 65,3 t/h.
Układ transportu popiołu spod elektrofiltrów oparty jest na pompach zbiornikowych - umieszczonych pod każdym lejem elektrofiltra. Popiół transportowany będzie bezpośrednio do zbiorników retencyjnych lub do zbiornika w stacji okresowego rozładunku popiołu przy istniejącej pompowni bagrowej. Rurociągi transportu pneumatycznego są poprowadzone na estakadzie zbiorczej.
ZBIORNIKI RETENCYJNE POPIOŁU
Popiół lotny gromadzony jest w trzech zbiornikach retencyjnych - każdy o pojemności użytecznej ok. Vu=20 000 m³ lub w zbiorniku awaryjnego zrzutu popiołu o pojemności użytecznej V=100 m³. Zbiorniki są wykonane jako żelbetowe.
Pod każdym zbiornikiem retencyjnym popiołu (żelbetowym) jest zlokalizowany zbiornik pośredni popiołu (stalowy), do którego poprzez układ rynien aeracyjnych podawany jest popiół ze zbiornika retencyjnego. Pod każdym zbiornikiem pośrednim są zlokalizowane układy załadunku popiołu na samochody i wagony oraz układ recyrkulacji popiołu.
Żelbetowe zbiorniki retencyjne popiołu wyposażone są w kompletne układy technologiczne pozwalające na między innymi na:
- załadunek popiołu do tych zbiorników;
- recyrkulację popiołu pomiędzy zbiornikami;
- załadunek popiołu na cysterny kolejowe oraz cysterny samochodowe;
Z każdego zbiornika retencyjnego popiół będzie można załadowywać (poprzez zbiornik pośredni) jednocześnie na dwie cysterny kolejowe lub jedną cysternę samochodową i jedną kolejową.
Obiekty układu wody chłodzącej wraz z chłodnią kominową tworzą zamknięty, zewnętrzny obieg wody chłodzącej, którego celem jest odebranie ciepła z kondensatorów, turbiny oraz wydzielanego przez urządzenia pomocnicze Bloku i wyemitowanie go do atmosfery wraz z oczyszczonymi spalinami przy użyciu mokrej chłodni kominowej o ciągu naturalnym.
Z uwagi na konieczność odprowadzenia bardzo dużej ilości ciepła obieg ten posiada nominalne obciążenie hydrauliczne wielkości Q=84 000 m3/h. Wymaga to stosowania dużych przekrojów przewodów, którymi przepływać będzie woda obiegowa oraz odpowiednio dużych pomp.
Z misy chłodni ochłodzona woda ujmowana będzie do komory krat gęstych i sit obrotowych. Komora ta jest monolityczną, żelbetową budowlą podziemną podzielona na dwie części, w których zainstalowane będą wyżej wymienione urządzenia.
Zastosowane na wlotach prowadnice umożliwiają zakładanie zastawek odcinających dowolną część komory.
Po oczyszczeniu w komorze sit, woda odprowadzona będzie podziemnym monolitycznym, żelbetowym, dwukomorowym kanałem ssawnym doprowadzających wodę do głównych pomp wody chłodzącej.
Pompownia wody chłodzącej składa się z monolitycznej, żelbetowej konstrukcji podziemnej, w której zlokalizowane są kanały napływowe pomp, pompy wraz z kompletnym osprzętem i wyposażeniem pomocniczym. Pompownia jest konstrukcją ciężką, przenoszącą obciążenia dynamiczne od pomp na podłoże gruntowe.
Z uwagi na konieczność zapewnienia niezbędnej wysokości zalania wirników, część podziemna posadowiona jest głęboko, na głębokości około 12,5 m pod poziomem terenu.
Silniki pomp ustawione na stropie pompowni powyżej projektowanego poziomu terenu wewnątrz hali będącej częścią nadziemną konstrukcji pompowni.
Do pompowni przylega:
- niezależny budynek rozdzielni elektrycznej wraz z pomieszczeniem AKPiA,
- budynek dla instalacji do chemicznej korekcji wody obiegowej oraz dla awaryjnej wody procesowej dla IOS.
Są to budynki posiadające części podziemne w postaci skrzyniowych, monolitycznych konstrukcji żelbetowych oraz części nadziemne o konstrukcji monolitycznej i murowanej z zewnętrznymi okładzinami ściennymi w postaci paneli z blach warstwowych.
Z pompowni woda tłoczona będzie do maszynowni i dalej do chłodni podziemnym rurociągiem z GRP (żywice poliestrowe wzmocnione włóknem szklanym) ułożonym ze spadkiem umożliwiającym jego odwadnianie.
Pod drogami, torami oraz na łukach rurociągi wyposażone będą w monolityczne, żelbetowe obudowy.
Miejsca, gdzie zainstalowane będą instalacje odpowietrzające wykonane będą jako obudowy w postaci żelbetowych komór.
Przed wejściem do chłodni na rurociągu przewidziano kompensator DN3400 umieszczony w żelbetowej podziemnej komorze.
Dane charakterystyczne:
- chłodnia kominowa z przepływem naturalnym, o żelazobetonowej konstrukcji skorupowej w kształcie hiperboloidy obrotowej typu Iterson.
- wysokość - 185 m
- średnica basenu - 143 m
- objętość basenu - 44,500 m³
- całkowita powierzchnia płaszcza - 5,5 ha
W zakresie budowy Bloku 11-tego Elektrowni Kozienice Polimex przygotował linie przesyłowe 400/110 kV na trasie wyprowadzenie mocy - rozdzielnia PSE. Linie te są podłączone do rozdzielni napowietrznych 400/110 kV od strony wyprowadzenia mocy, których konstrukcja opiera się na wyłącznikach i przekładnikach pomiarowych z zastosowaniem izolacji sześciofluorku siarki. Umożliwiło to zapewnienie niezawodnej pracy urządzeń, jak również znaczącą oszczędność miejsca. Zamontowane transformatory są połączone szynoprzewodami z wyłącznikiem generatorowym, który z kolei jest podłączony do wyjścia mocy z generatora. Sam wyłącznik generatorowy jest unikalną konstrukcją, gdzie po raz pierwszy zastosowano oddzielne bieguny dla każdej z faz. Podyktowane to zostało bardzo dużą mocą generatora znacznie przewyższającą 1 GW. Dlatego też transformator wyprowadzenia mocy również podzielono na 3 niezależne transformatory, łączone tylko w punkcie neutralnym. Takie rozwiązanie pozwala nie tylko na zmniejszenie konstrukcji, ale również na bardziej elastyczne prowadzenie eksploatacji. W przypadku awarii łatwo jest wymienić jeden z transformatorów (rezerwowy jest składowany w pobliżu zespołu wyprowadzenia mocy). Całość przedstawia eleganckie rozwiązanie inżynierskie, ale również stanowić będzie bardzo wygodny układ do wieloletniej bezawaryjnej pracy.