Ribbon-cutting ceremony in the new plant Polimex-Mostostal Steel Product Manufacturing and Paint Shop in Siedlce.
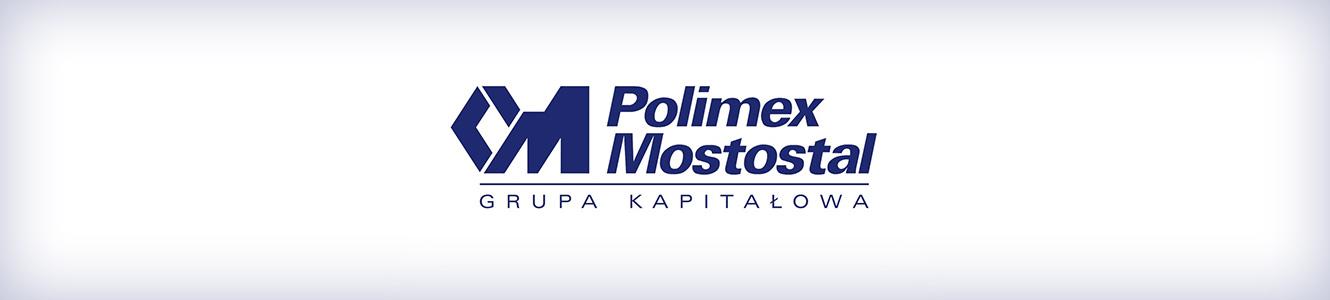
The project covered by the program for extension of production capacities adopted already by the Management Board of Polimex-Mostostal in 2008 for both the Company and the entire Group has just been completed.
Production in the new plant – Steel Product Manufacturing and Paint Shop – was launched on 5th November this year.
Erection of the new unit was started in September 2008. The investment was set up within organization structures of the Special Economic Zone of Tarnobrzeg and its overall value was about PLN 260 m. New facilities were erected on a plot with the area of 12.5 ha, just nearby the existing plant of Polimex-Mostostal S.A. in Siedlce, at Terespolska St.
- Owing to the new plant we have 60% more production capacities in the area of highmargin steel structures and hot-dip galvanizing. We have become even more competitive in the sectors of manufacturing and services. I am sure that this investment shall be really profitable for the entire Company - adds Mr Konrad Jaskóła.
- Polimex-Mostostal S.A., within framework of the new investments, has launched really up-to-date technological lines, developed manufacturing capacities for heavy steel structures, and applied highly-efficient equipment for machining and processing of materials and subassemblies with further coating and painting. In addition, new software to aid management of the manufacturing process was implemented. Putting the project in operation also means improvements in occupational health and safety for all the staff, better working conditions and increased care for environment protection – informs President Jaskóła.
The building Company Laying the groundbreaking plaque for erection of a new plant – Steel Product Manufacturing and Paint Shop in Siedlce.
The ceremony of laying the groundbreaking plaque that took place on 29th September 2008 was attended by Mr Dariusz Piątek, Deputy Governor of Mazovia Province, Ms Marta Sosnowska and Mr Jarosław Głowacki, Deputy Presidents of Siedlce, the Reverend Janusz Wolski, provost of the St. Spirit Parish, MPs Mr Jacek Kozaczyński and Mr Krzysztof Tchórzewski, Mr Marek Indyk, Branch Director of the Agency for Industry Development in Tarnobrzeg, the Special Economic Zone of Tarnobrzeg EURO-PARK WISŁOSAN, Ms Magdalena Leszczyńska and Ms GraŜyna Dobrowolska, representatives of the PKO Bank Polski (PKO Bank of Poland) that cofinanced the investment, Ms Zofia śuk, Chancellor of the Business Centre Club Lodge in Siedlce, Mr Kazimierz Klęk, President of the Supervising Board in Polimex, Mostostal, Mr Zygmunt Wielogórski, County Head of Siedlce, representatives of companies that collaborate with Polimex-Mostostal, and last but not least, the Management Board of the Company.
The new plant – Steel Product Manufacturing
The newly erected plant has increased production capacities of the Company by 3,000 tons per month. Thus, the overall production of the Steel Product Manufacturing Division shall exceed 6,100 tons per month. It strengthens the position of Polimex-Mostostal among European leaders of companies that deal with assembling of steel structures. The new unit is furnished with cutting edge equipment and the most advanced technologies: an automatic plant for profile handling, laser stands for steel sheet handling, modern oxygen and plasma cutting machines for steel sheets that enable handling steel sheets with as large dimension as 150 mm by thickness, 2,500 mm by width and 30,000 mm by length with no need to join steel sheets down their lengths as well as shot-blasting machines, a high-productivity line for welding of plate girders, welding semi-automats with the functionality to monitor welding parameters.
As the plant is furnished with modern hoisting equipment it is able to cope with single components of their weight up to 64 tons. Maximum dimensions for industrial shops that can be pre-assembled indoors are 80 meters by length, 25 meters by width and 7 meters by height (dimensions are limited by the size of the assembly bay).
It enables to assemble all types of structures for power engineering, steelwork industry, petroleum chemistry and other chemical sectors, flue gas purification plants, incineration plants, mining industry, telecom sector, road engineering (bridges, walkway platforms, flyovers), automotive industry as well as for public buildings (shopping malls, supermarkets, sport facilities, panorama towers) as well as manufacturing and warehousing shops, support structures for technological plants, pipelines and support structures.
The new Plant for Corrosion Protection: Hot-Dip Galvanizing Shop and Paint Shop Hot-dip galvanizing shop.
The hot-dip galvanization process consists in formation of a corrosion-resistant zinc coat on exposed surfaces of steel structures. That coat is applied by immersion of appropriately prepared steel parts into a hot bath of liquid zinc.
Hot-dip galvanization services pose a significant part of the overall commercial offer of the Company. This service has been being provided by the plant in Siedlce for more than 30 years with use of two technological paths. Similar services are offered by other hot-dip galvanizing plants owned by Polimex-Mostostal and operated in Częstochowa and Dębica. The new hot-dip galvanizing plant in Siedlce increases production capacities of the Plant for Corrosion Protection by 4,000 tons of galvanized products per month. It makes a difference for our customers as they can take advantage of our services even quicker and more efficiently. Our galvanizing plant apply technical and technological solutions that are the most appropriate in terms of cost-efficiency and environment protection as we minimize detrimental effect of technological processes onto the environment by application of the following measures:
- HCl vapour absorbers that reduce emission of hydrogen chloride vapours into atmospheric air;
- air filters that capture 99.9% of dust from above the galvanizing tank mirror and prevent from its emission to the atmosphere;
- equipment for recycling and reclamation of the flux bath to reduce release of industrial liquid wastes and bring down consumption of chemicals;
- special additives to the zinc bath that improve quality of final zinc coats and cut down consumption of chemicals.
The new plant is designed to hot-dip galvanize steel parts in the melted zinc bath at temperature up to 460°C. The galvanizing tank with its length of 9 m is capable to fit about 320 tons of liquid zinc. Application of an advanced control system enables visualization and on-line supervision of the galvanization process via the plant intranet Paint shop The paint shop is designed to paint steel structures and products with use of the hydrodynamic method. Modern equipment and total area of the plant as high as nearly 8,000 sq. m. make it possible to paint large-dimension products and structures, and even entire public facilities, such as industrial shops, bridges, etc. Throughput of the paint shop is 2,500 tons of products that can be monthly coated with paints and other agents. The plant is equipped with two shot-blasting machines, namely a chamber one and a turbine one. That equipment enables preliminary preparation for anticorrosive protection not only simple and large parts, but also 3D structures with sophisticated design. Maximum dimensions of coated products are the following: length = 28 m, width = 6 m, height = 5 m and the maximum unit weight is 64 tons.
New Plants in figures.
1. Erection time: September 2008 – October 2009.
2. Target employment: more than 350 people
3. Specification of the investment:
No. | SPECIFICATION | UNIT | Q-TY |
---|---|---|---|
1 | Area of the investment plot | ha | 12.56 |
2 | Built-up area of manufacturing shops | m2 | 37 018 |
3 | PArea of social and office buildings | m2 | 4 371 |
4 |
Area of roads, parking lots and paved squares |
m2 | 40 108 |
5 | Area of trestle bridges for raw steel products and final production | m2 | 10 990 |
6 | Macrolevelling of the area – embankment | m2 | 127 121 |
7 | Cast structures of reinforced concrete | m3 | 17 710 |
8 | Pre-fabricated structures of reinforced concrete | m3 | 1 061 |
9 | Steel structures | t | 3 288 |
10 | Overhead travelling cranes for transportation of suspended loads | sz | 33 |
11 | Total length of tracks for overhead cranes | mb | 2 031 |
12 | Total length of tracks for shuttle trolley transport | mb | 853 |
13 | Total area of wall siding | m2 | 18 175 |
14 | Total length of underground utility networks - rainwater sewer - wastewater sewer - central heating and central technological heat supply - natural gas supply - MV power cables |
mb mb mb mb mb |
3 665 1 942 4 097 222 14 700 |
15 | Total length of indoor utility systems - water supply - electric network - compressed air network - network of technical gases - ventilation ducts |
mb mb mb mb mb |
1 655 160 100 2 384 6 174 4 750 |
16 | Number of parking places - trucks - passenger cars |
szt. szt. |
22 340 |
4. Technological process in the Steel Product Manufacturing Plant
4.1 Production capacity: 3000 t per month
4.2. Maximum weight of a single unit: 64 tons
4.3. Maximum dimensions of a single unit: width – 6.2 m height – 4.2 m length – 30.0 m
4.4. Specification of machinery and production paths:
· highly efficient CNC equipment for cutting and drilling,
· mechanized operation of steel sheet bevelling,
· automatic welding process for steel sheet profiles,
· automatic process for rolled profiles treatment (cleaning, cutting, drilling, marking),
· post-assembly welding with use of the most advanced equipment capable to monitor parameters of the welding process.
5. Process of corrosion protection by hot-dip galvanizing
5.1 Production capacity: 4,000 tons per month,
5.2 Maximum weight of a single unit for galvanization 7.0 t
5.3 Maximum dimensions of a single unit: width - 1.5 m height - 3.0 m length - 8.5 m
5.4 Protective processes and appliances:
- application of inhibitors for etching in a hydrochloride acid in order to reduce consumption of the acid and emission of HCl fumes,
- elimination of lead, typically used as a protective coat on the bottom of the galvanization tank,
- application of absorbers for HCl fumes,
- application of air filters capable to capture 99.9% of dust from above the galvanization tank to prevent from its emission into the atmosphere,
- application of equipment for recycling and reclamation of the flux bath to reduce release of industrial liquid wastes and bring down consumption of chemicals,
- use of natural gas to fire zinc melting furnaces in order to reduce pollutant emission into the atmosphere.
6. Process of corrosion protection by painting
6.1 Area of the paint shop: 7,970 m²
6.2 Production capacity: 2,500 tons per month,
6.3 Maximum weight of a single unit for: 64 tons
6.4 Maximum dimensions of a single unit: width - 6.2 m height - 4.2 m length - 30.0 m
6.5. Application of paint coatings by means of the hydrodynamic method.
6.6 Preparation and pre-treatment of surfaces to be painted by:
- degreasing operation – to be carried out in washing stands located nearby shot-blasting machines,
- cleaning operation – to be carried out with use of one shotblasting machines (as needed), a chamber one or a turbine one.
6.7. Heating and ventilation of the paint shop is carried out with use of ventilating and heating turbines as well as exhausting radial fans.
Convoluted growth of both the Company and the Group
- Convoluted growth is a factor that supports satisfying and dynamic development of both the Company and the entire Group. The largest projects that have been completed in 2009 include extension of production capacities in Siedlce, in the Boiler Factory SEFAKO in Sędziszów as well as in the pre-fabrication plant of pipeline components Energop in Sochaczew owned by EnergomontaŻ Północ. Total expenditures for the projects amounted to about PLN 400 m. Projects in Siedlce and Sędziszów were completed within structures of Special Economic Zones headquartered in Tarnobrzeg and Starachowice. It is a benefit that enable tax rebates and consequently increases profitability of investments – says Konrad Jaskóła.
- In 2009 we have invested PLN 140 m. to get 60% growth of production capacities in the Steel Product Manufacturing Plant in Siedlce. In turn, expenditures at the level of ca. PLN 30 m. at the plant in Siedlce have made it possible to increase manufacturing of platform meshes by 50%. As about corrosion protection, we are just about to launch a modern plant for hot-dip galvanizing, where the plant is worth more than PLN 80 m. Thus, the overall Expenditures for the operations in Siedlce reached about PLN 260 m. – says Konrad Jaskóła.
Sefako.
The investment program for Sefako has just been completed, where about PLN 70 m. was spent for erection of a new assembly shop. The new facilities make it possible to double the number of manufactured power boilers. The opening ceremony of the new assembly shop was held on 4th September this year. The facilities were erected under auspicious of the Special Economic Zone of Starachowice. Nearly 19 ha of total area covered by the factory facilities (with 4 ha assigned for the new project) rates the Boiler Factory SEFAKO S.A. as one of the larger manufacturer of boilers and their components worldwide. It is also one of crucial investments in Świętokrzyskie Province over the recent years and is expected to offer about 300 new jobs. In addition to the manufacturing shop the investment package includes an office and social building, a laboratory for X-ray examination and a technical building. The new shop is designed for assembling of boilers and power equipment, with final water tests, commissioning, approvals and dispatching to customers via new logistic nodes of the factory.
Energop.
Extension of the pipeline prefabrication plant Energop seated in Sochaczew and owned by the Mostostal Group has just come to the end. Overall value of the project that lasted from 2008 to 2009 is about PLN 20 m. PLN. The most important part of the project was greenfield erection of the Surface Treatment Division that is made up of a shot-blast plant and a paint shop. Due to application of up-to-date shot-blasting chambers (there are only few similar systems in Poland), Energop is capable to become much ahead of their competitors. Owing to the new investment Energop shall be able to prefabricate ca. 10 th. tons of pipelines, instead of current 6 th. tons. The company from Sochaczew shall also extend their production series and fabricate their pipelines of more sophisticated steel grades. The foundation stone for the Surface Treatment Division was laid on 8th May 2008.
- Our investment projects result in renovation of the machinery stock, more efficient manufacturing processes and increased production capacities. It is why this year we could increase production capacities in the area of high-margin steel structures, power boilers for various types of fuel, pipelines as well as services of hot-dip galvanizing. Tax rebates granted to the Company and amounted to of 40% of the investment value in Siedlce and Sędziszów are also an essential factor, we can obtain such benefits because we implemented our investments within framework structures of Special Economic Zones – adds President Jaskóła.
Polimex-Mostostal Design and Development Centre.
This year Polimex-Mostostal has extended its design and development potential. The Company considers it as one of their priorities so it set up and launched a multisectoral design office in Gliwice. The Design Centre is a renowned, modern and efficiently working engineering enterprise that takes advantage of more than 5o year experience of its ancestors. The Centre deals with development of engineering documentation for various sectors, including chemistry, power engineering and road infrastructures – motorways and highways. Current employment of the office is about 300 of highly qualified designers.
- Launching of an own Design Centre is our respond to really scarce development potential that always used to be a ‘bottleneck’ and prevented us from completion of projects on time. Moreover, still more and more investments are subcontracted according to the formula ‘design and erect’. The Polimex-Mostostal Design Centre shall contribute to further increase of competitiveness demonstrated by our offers at tenders – informs Konrad Jaskóła
Domestic demand.
Starting from beginning of this year Polimex-Mostostal concluded a number of contracts, including contracts for execution of large projects, e.g.:
- construction of the ‘B’ segment of the A2 motorway from Stryków to Konotopa, with the gross contractual price of nearly PLN 844 m.
- delivery and assembly of steel structures as well as installation of equipment for the coal feeding system in Bełchatów electric power plant for the net price of nearly PLN 84 m.
- construction of a segment of the A1 motorway from Sośnica exit to Maciejów exit for the net price of nearly PLN 900 m.
- long-term contract for reconstruction of the ‘Wisła’ stadium in Cracow with the price of jobs that are to be carried out therein amounting to PLN 900 m. net value.
- erection of the Museum for History of Polish Jews with the location in Warsaw for the net price of PLN 125 m.
- delivery and assembly of steel structures in Neurath electric power plant in Grevenbroich (Germany) for the net price of more than PLN 55 m.
- erection of a new exposition hall and a reception and lobby building on the area of Fairs in Kielce for the net price of more than PLN 35 m.
- reconstruction of Wyszyńskiego St. in Gorzów Wielkopolski which is one of the most important communication arteries in the town. The net price of the contract is PLN 18 m.
- upgrade of the railway line from Warsaw to Gdynia, where the contract for the price of more than EUR 250 m. was concluded by the consortium with participation of Torpol – a 100% subsidiary company of Polimex-Mostostal.
Prospects for new contracts.
- Conclusion of contracts with completion deadline during the next year and few subsequent years has become one of the most important tasks for marketing staff. Step-by-step, we are filling our portfolio with new assignments – emphasizes Mr Konrad Jaskóła.
- Power engineering is one of the most promising and innovative sectors of the economy. Polimex-Mostostal has wide experience in that area and strong position as a general contractor. When we were developing our strategy for incoming years, we obviously took account for prospects that seem to be pretty bright for the entire sector so we have to actively participate in its growth. Polimex-Mostostal offers turnkey execution of power engineering projects, chiefly as a general contractor for investments – informs Mr Konrad Jaskóła.
- We collaborate with well-recognized, key worldwide leaders in the power engineering sector, such as Alstom Power, Tecnimont SpA, BWE, Siemens, Austrian Energy. Our portfolio includes contracts for largest Polish and foreign power engineering companies. Currently we are involved in assignments for the electric power plant in Bełachatów, heat and power generating plant śerań, electric power plants Neurath and Westfallen (Germany). We are just awaiting some new large orders.
- Despite the foregoing project we are keen to become an operator in the power engineering sector. It is why we concluded a contract with the PGNiG (Polish Oil and Gas Mining Ltd.), Nitrogen Factory S.A. in Tarnów – Mościce and Tauron Polska Energia S.A. (Tauron Polish Energy Ltd.) to erect a new heat and power generating plant with power of 200 MW that shall generate power from combustion of natural gas. We believe that when the Company becomes an operator in the power engineering sector or in the communication infrastructure it will be a long-term business with satisfying return rates and it shall allow further diversification of business activities that our Company is involved in. Such an approach to own development was already successfully applied by companies that are quite similar to our enterprise – explains President Jaskóła.
- We submit many offers that win tenders. Let me only mention two of them that proved to be the most beneficial for investors:
· the offer with the gross price of PLN 80 m. for construction of the road to connect Surzyckiego and Christo Botev streets in Cracow,
· the offer for the price above PLN 121 m. for turnkey construction of the haulage system for the Lublin Coal ‘Bogdanka’ S.A.
However, in the both cases our opponents appealed against the tender results. We hope that the appealing procedure shall soon end up according to our intentions and we shall sign those contracts in near future – informs Mr. President Jaskóła.
· what is important, The General Directorate for National Roads and Motorways (GDDKiA) appointed our offer for construction of a subsequent A4 motorway segment from Szarów to Brzesko as the best one – adds the President.
Steady and strong position of Polimex-Mostostal Results of both the Company and the Group correspond to previous assumptions and achieved rates of profit growth are even higher that they were anticipated in former plans.
The last balance of financial results for the recent 9 months of this year is really satisfying. Both sales and net profit increased as compared to the corresponding period of the previous year.
We expect that this year, in spite of a general slowdown of economy, shall be completed with results even better than we had expected and our net profit shall grow by ca. 15% as compared to the year 2008.
The Management Board has developed and is implementing the program that is intended to make order in the structure of the Polimex-Mostostal Group with the aim to acquire more shares of profitable companies where Polimex-Mostostal is already the major shareholder.
The plan for refining the organization structure is dedicated to the following key companies of the Group: EnergomontaŜ Północ, Naftobudowa S.A., Nafroremont Co. Ltd., but also ZRE Cracow Co. Ltd., ZRE Lublin Co. Ltd., EPE Rybnik Co. Ltd., a and ECE Remont Co. Ltd. The agreements that were already concluded between companies define preconditions and rules of the restructuring process, including provisions for merges and acquisitions. The merging process shall consist in transfer of assets previously owned by acquired companies to Polimex-Mostostal in return for shares of Polimex-Mostostal that shall be distributed among minor shareholders of these companies.
The restructuring process shall bring the following benefits:
- full consolidation of business results achieved by the merged companies,
- taking better advantage of the synergy effect between companies within the Group and simplification of the organization structure of the Group itself as well as making the management process in the Group more flexible. Simplification of the structures shall make the Group more transparent and clear for analytics and the stock exchange market,
- unification of management systems and accurate allocation of competences within the organization structure,
- strengthening of the Group position as a national leader in all the areas where the Group runs its business,
- reduction of the management overheads,
- making all the services offered and provided by the Group more complementary to achieve market domination in profit-promising sectors,
- increase of free float of Polimex-Mostostal shares on the Warsaw Stock Exchange (GPW),
- growth of the bidding efficiency owing to extended spectrum of offered services that can be provided unaidedly with use of the scale effect,
- cost effective utilization of human and equipment redundant resources by allocation of them to promising sectors.
- getting rid of business fluctuations from one season to another,
- elimination of internal competition between entities that are members of the same Group,
Polimex-Mostostal and its Management Board are appreciated with awards and honours
In 2009 Polimex-Mostostal S.A. and its President of the Management Board have been awarded with the following prizes and honours:
- · Polish Award of Quality for Polimex-Mostostal in the 15th edition of the competition organized by the National Chamber of Economy, Polish Centre of Examination and Certification and Polish Forum ISO 9000 [October 2009].
- Polish Award of Quality ‘Perfect Leader’ for Konrad Jaskóła, President of the Management Board in the 3rd edition of a competition organized by National Chamber of Economy, Polish Centre of Examination and Certification and Polish Forum ISO 9000 [October 2009].
- Honorable title ‘Leader of Polish Transformation’ for Polimex –Mostostal in the ranking ‘20 years of Polish Transformation’ (for the category ‘Infrastructure and Civil Engineering’) organized by Forbes monthly [16th September 2009].
- Honourable title ‘Ambassador of Polish Economy” for the category ‘European Brand’ for Polimex-Mostostal S.A. in a competition organized by Business Center Club under honourable patronage of the Foreign Affairs Minister of Republic of Poland [June 2006].
- 1st place in the group of WIG 20 (Warsaw Stock Exchange Index 20) in the ranking TOP TSR (Total Shareholder Return) 2004 - 2008 of the Top Manager Magazine for CEOs (Chief Executive Officers) [June 2009].
- 3rd place among 100 of the Most Valuable Companies in Poland in 2008 for the civil engineering sector. Ranking of Newsweek and Atkearney Journals [27.04.2009].
- Honourable Title and Statuette of ‘Diamond Engineer’ for Konrad Jaskóła – President of the Management Board – granted by the jubilee, 15th voting of readers ‘Przegląd Techniczny’ (‘Technical Review’) engineers magazine [27th February 2009].
- Medal in memory of prof. Stanisław Pilat for Konrad Jaskóka, President of the Management Board for many years of efforts devoted to development of oil industry in Poland and many years of creative collaboration with the Institute of Oil Technology granted by the Medal Chamber in consultation with Director of the Institute of Oil and Gas and Scientific Board of the Institute of Oil and Gas [January 2009].